This article is an introduction to spoilboards - what they are, why they are needed and what material is recommended to use.
< Previous | List | Next >
A spoilboard is a disposable work surface mounted on top of the Y Bench. It sits underneath the stock material and is clamped between the rollers of the Upper and Lower X Beams.
You can adjust the position of the rollers on the Upper X Beam by pushing them, so that they make contact with the spoilboard and stock material.

The spoilboard has three main functions:
-
Protect SmartBench from damage when the tip of the cutter breaks through the bottom surface of your work piece.
-
Become a large format work holding surface which can be easily removed when SmartBench is not in use.
-
Improve the surface finish on the underside of your workpiece.

|
Spoilboards improve the finish on your work by providing another solid surface for the cutter to work against as it breaks through the bottom of your stock material.
|
How do I choose the correct spoilboard?
Many different materials can be used as spoilboards. When selecting a suitable spoilboard, it is important to choose something that is:
-
Rigid
-
Flat
-
Bigger than your stock material
-
Cost effective
-
Smooth - especially on the bottom
-
Ideally have a straight edge that can be aligned with the Y axis.

|
We recommend using a 6mm (1/4’’) or 9mm (3/8’’) double melamine faced MDF board.
|
Important: use a smooth board!
The spoilboard MUST be smooth enough that:
-
The Lower X Beam rollers can make full contact with it throughout the entire job.
-
The X Beam can securely clamp both spoilboard and stock material firmly together, with no movement or unevenness during operation.
-
The beam rollers can run easily along the length of the spoilboard, with no resistance.
Top surface of spoilboard
The top surface of the board should be flat and smooth enough that the stock material:
It is ok to reuse a spoilboard that has been cut into from a previous job, provided it meets these requirements.

Bottom surface of spoilboard
The lower rollers need to run along a flat and smooth surface. A smooth flat surface is essential to:

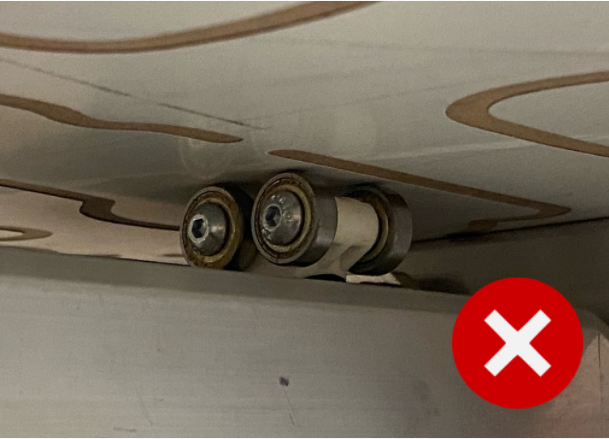
< Previous | List | Next >